Remote locations and big capital investments are very common elements of mining projects whether they are in remote North Western Australia, the South Island of New Zealand or a tropical island in the Pacific. Equipment reliability is absolutely critical to protect the investment and maintain production.
Temperzone has locally designed, manufactured and supported mining projects in Australia, New Zealand and the Pacific for many years. We have designed manufactured and supported air conditioning equipment for use in some of the harshest environments on the planet. The Woodside Energy Pluto LNG processing plant is an excellent example of how Temperzone works closely with the mining sector.
When you have a multi-billion dollar LNG processing plant in remote North Western Australia, plant reliability is critically important. Temperzone has just designed, manufactured and supplied six custom package units to be installed in the Woodside Energy Pluto LNG processing plant on the Burrup Peninsula in North Western WA.
The new package units are replacements for the legacy units supplying air conditioning to the Harmonic Filter (HF) switch rooms which are critical to the processing plant operation. The replacement is required because the original air conditioning equipment, which was built overseas, is now 9 years and old has become unreliable. Compounding the reliability issues, spare parts have become hard to obtain.
An additional challenge to the project is that the Woodside LNG plant sits on the narrow Burrup Peninsula with Indian Ocean salt water immediately adjacent to the plant on both sides. High temperatures, high humidity and high salt levels make this a particularly difficult environment for air conditioning equipment.
Not only are we able to understand the requirements of mechanical and electrical engineers but also the mechanical contractors and installers. The solution was extremely customised air cooled package units consisting of:
- EC plug fans with Modbus monitoring
- Temperzone system control boards (UC8) for Modbus monitoring
- 316L stainless steel casing, wiring labels, logos, screws, hinges and door latches
- Duty/standby dampers and explosion proof damper motors. Dampers are on the outside of the units to allow for them to be left in place should a whole unit need to be replaced. This meant having to insulate the dampers and have custom flanges to allow to insulate without fouling on the damper linkages.
- Copper finned, electro-tinned and Blygold coated condenser coils (corrosion resistance)
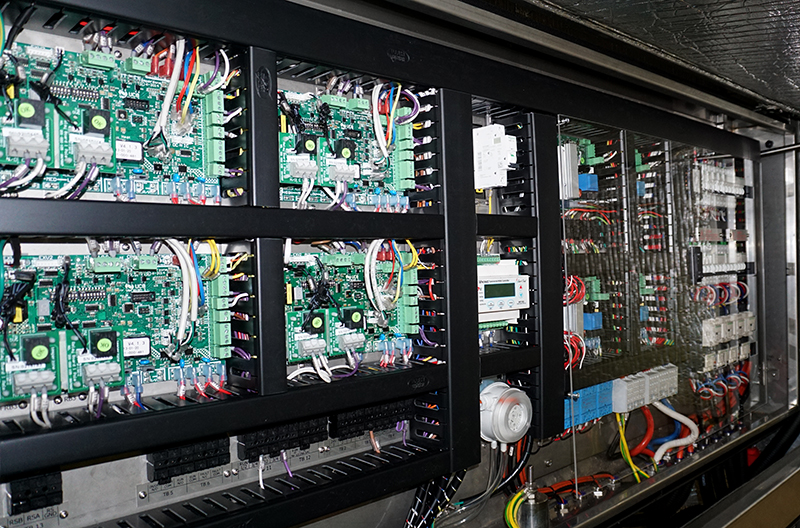
- Upgraded switchboard with:
- IP56 rating
- Pressurized with cooled and filtered air from evap chamber.
- Separated low and high voltage components,
- High voltage components covered with a escutcheon plate. Access to circuit breakers has been cut in the plate.
- Dirty filter DP switch
- Upgraded unit wiring with all cables run within the unit protected with stainless steel and rubber coated conduits.
- ArmaChek-R insulation protection on all insulated pipework
Extreme Corrosion Resistance
These package units are some of the most corrosion resistant air conditioning units ever manufactured in Australia and will be connected to 3mm 316 Stainless Steel ductwork on site.
The six units form a Duty / Standby array which automatically moves units from standby to duty if there is a failure. Units are controlled via a Smarttemp Viiking controller working directly with the Temperzone UC8 controller board. Additional control is enabled via Modbus.
The units were designed and manufactured at Temperzone’s Australian manufacturing facility in Sydney before freighting to WA.
Pre installation unit testing was done at Airskill in Perth. Units are wired up with a main air conditioning control panel allowing High Pressure, Vacuum, Electrical and Run Testing to be done with Woodside Inspectors present.
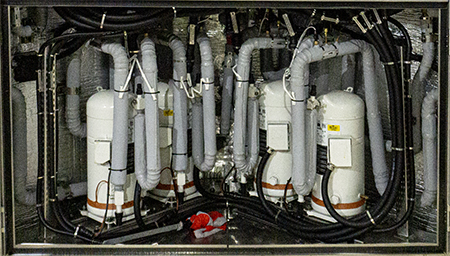
Local design, local manufacture and local support, with a focus on reliability makes Temperzone the obvious air conditioning partner for the Mining Sector in Australia New Zealand and the Pacific.